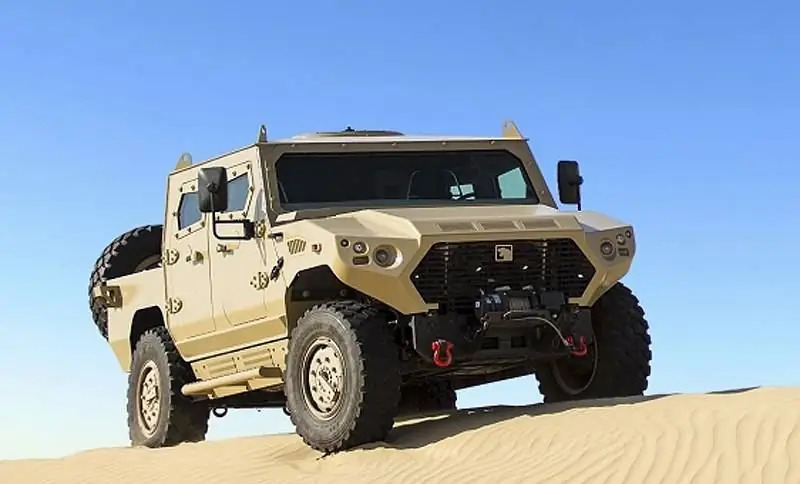
Brnění je o miliony let starší než lidstvo a bylo vyvinuto především k ochraně před čelistmi a drápy. Je možné, že krokodýli a želvy by mohly částečně inspirovat lidi k vytváření ochranných prvků. Všechny zbraně kinetické energie, ať už jde o pravěký kyj nebo průbojný projektil, jsou navrženy tak, aby soustředily velkou sílu na malou oblast, jejím úkolem je proniknout do cíle a způsobit mu maximální poškození. Úkolem pancíře je tedy zabránit tomu odkloněním nebo zničením útočných prostředků a / nebo rozptýlením energie nárazu na co největší plochu, aby se minimalizovalo jakékoli poškození lidské síly, transportních systémů a struktur, které chrání.
Moderní brnění se obvykle skládá z tvrdé vnější vrstvy k zastavení, vychýlení nebo zničení střely, mezivrstvy s velmi vysokou „prací na rozbití“a viskózní vnitřní vrstvy zabraňující vzniku trhlin a úlomků.
Ocel
Ocel, která se stala prvním materiálem široce používaným při výrobě obrněných vozidel, je stále žádaná, a to navzdory vzniku brnění na bázi lehkých slitin hliníku a titanu, keramiky, kompozitů s polymerovou matricí, vyztužených skelnými vlákny, aramidu a polyetylen s ultra vysokou molekulovou hmotností, jakož i kompozitní materiály s kovovou matricí.
Mnoho oceláren, včetně SSAB, pokračuje ve vývoji vysokopevnostních ocelí pro různé aplikace kritické z hlediska hmotnosti, jako je další opláštění. Obrněná ocel ARM OX 600T, dostupná v tloušťkách 4-20 mm, je k dispozici se zaručenou tvrdostí 570 až 640 jednotek HBW (zkratka pro Hardness, Brinell, Wolfram; test, při kterém se lisuje wolframová koule standardního průměru do vzorku materiálu se známou silou, pak se změří průměr vytvořeného vybrání; poté se tyto parametry nahradí vzorcem, který vám umožní získat počet jednotek tvrdosti).
SSAB také zdůrazňuje důležitost dosažení správné rovnováhy tvrdosti a houževnatosti pro ochranu proti průniku a protržení. Jako všechny oceli, ARMOX 600T se skládá ze železa, uhlíku a řady dalších legujících složek včetně křemíku, manganu, fosforu, síry, chromu, niklu, molybdenu a boru.
Použitá výrobní technika má svá omezení, zejména pokud jde o teplotu. Tato ocel není určena k dodatečnému tepelnému zpracování; po zahřátí nad 170 ° C po dodání nemůže společnost SSAB zaručit její vlastnosti. Společnosti, které mohou tento druh omezení obejít, pravděpodobně přitahují podrobnou kontrolu výrobců obrněných vozidel.
Další švédská společnost Deform nabízí výrobcům obrněných vozidel, zejména těm, kteří chtějí zlepšit ochranu užitkových / civilních vozidel, součásti za tepla odolných vůči pancéřování.
Jednodílné Deform firewally jsou instalovány v Nissan PATROL 4x4, minibusu Volkswagen T6 TRANSPORTER a pickupu Isuzu D-MAX spolu s pevnou podlahovou deskou ze stejného materiálu. Proces tváření za tepla vyvinutý společností Deform a používaný při výrobě plechů si udržuje tvrdost 600 HB [HBW].
Společnost tvrdí, že dokáže obnovit vlastnosti všech pancéřových ocelí na trhu při zachování strukturálně definovaného tvaru, přičemž výsledné části daleko převyšují tradiční svařované a částečně se překrývající konstrukce. V metodě vyvinuté společností Deform jsou plechy kaleny a temperovány po kování za tepla. Díky tomuto procesu je možné získat trojrozměrné tvary, které nelze získat tvářením za studena bez povinných v takových případech „svarů, které narušují integritu kritických bodů“.
Deformované ocelové plechy tvářené za tepla byly použity na BAE Systems BVS-10 a CV90 a od počátku 90. let na mnoha strojích Kraus-Maffei Wegmann (KMW). Přicházejí objednávky na výrobu trojrozměrných pancéřových plechů pro tank LEOPARD 2 a několika tvarových plechů pro vozidla BOXER a PUMA, plus pro několik vozidel Rheinmetall, včetně opět BOXER, a také poklopu pro vozidlo WIESEL. Deform funguje také s jinými ochrannými materiály, včetně hliníku, kevlaru / aramidu a titanu.
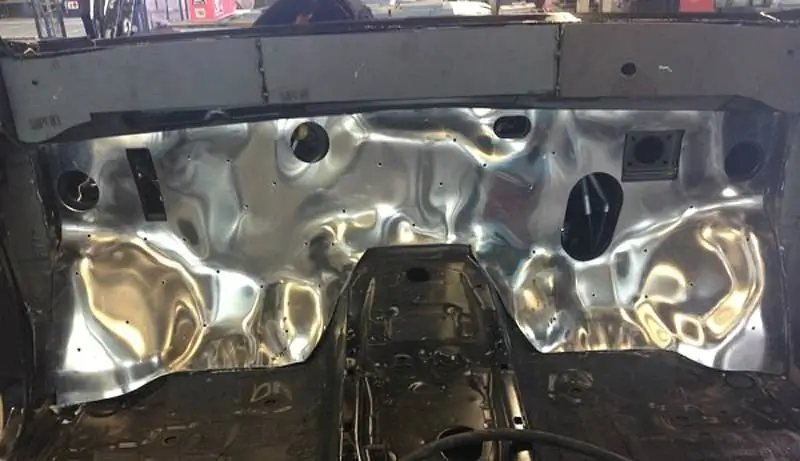
Hliníkový pokrok
Pokud jde o obrněná vozidla, poprvé bylo hliníkové brnění široce používáno při výrobě obrněného transportéru M113, který se vyráběl od roku 1960. Byla to slitina označená 5083, obsahující 4,5% hořčíku a mnohem menší množství manganu, železa, mědi, uhlíku, zinku, chromu, titanu a dalších. Přestože si 5083 po svařování dobře zachovává svoji pevnost, nejedná se o slitinu tepelně zpracovatelnou. Nemá tak dobrou odolnost jako 7,62 mm průbojné střely, ale, jak potvrdily oficiální testy, zastaví 14,5 mm průbojné střely sovětského typu lépe než ocel, přičemž šetří váhu a dodává požadovanou pevnost. Pro tuto úroveň ochrany je hliníkový plech silnější a 9krát pevnější než ocel s nižší hustotou 265 r / cm3, což má za následek snížení hmotnosti konstrukce.
Výrobci obrněných vozidel brzy začali požadovat lehčí, balisticky silnější, svařitelné a tepelně zpracovatelné hliníkové brnění, což vedlo k vývoji společnosti Alcan 7039 a později 7017, obojí s vyšším obsahem zinku.
Stejně jako u oceli může i ražení a následná montáž negativně ovlivnit ochranné vlastnosti hliníku. Při svařování tepelně ovlivněné zóny změknou, ale jejich pevnost se částečně obnoví díky kalení během přirozeného stárnutí. Struktura kovu se mění v úzkých zónách poblíž svaru, což vytváří velká zbytková napětí v případě chyb při svařování a / nebo montáži. V důsledku toho by je měly výrobní postupy minimalizovat a zároveň by mělo být minimalizováno riziko korozních trhlin způsobených napětím, zvláště když se předpokládá životnost konstrukce stroje více než tři desetiletí.
Korozní praskání napětím je proces vzniku a růstu trhlin v korozivním prostředí, který má tendenci se zhoršovat se zvyšujícím se počtem legujících prvků. K tvorbě trhlin a jejich následnému růstu dochází v důsledku difúze vodíku podél hranic zrn.
Stanovení náchylnosti k praskání začíná extrakcí malého množství elektrolytu z trhlin a její analýzou. Provádějí se zkoušky korozní zátěže s nízkým napětím, aby se zjistilo, jak moc byla konkrétní slitina poškozena. Mechanické natahování dvou vzorků (jeden v korozivním prostředí a druhé v suchém vzduchu) probíhá, dokud selže, a poté se porovná plastická deformace v místě zlomeniny - čím více je vzorek natažen k porušení, tím lépe.
Odolnost proti koroznímu praskání napětím lze zlepšit během zpracování. Například společnost Total Materia, která si říká „největší databáze materiálů na světě“, Alcan zlepšil výkon 7017 v testech zrychleného korozního praskání napětím 40krát. Získané výsledky také umožňují vyvinout metody ochrany proti korozi pro zóny svařovaných konstrukcí, ve kterých je obtížné vyhnout se zbytkovým napětím. Výzkum zaměřený na zlepšení slitin za účelem optimalizace elektrochemických charakteristik svařovaných spojů pokračuje. Práce na nových tepelně zpracovatelných slitinách se zaměřuje na zlepšení jejich pevnosti a odolnosti proti korozi, zatímco práce na slitinách, které nejsou tepelně zpracovatelné, si klade za cíl odstranit omezení vyplývající z požadavků na svařitelnost. Nejtvrdší materiály ve vývoji budou o 50% pevnější než nejlepší hliníkové brnění, které se dnes používá.
Slitiny s nízkou hustotou, jako je lithiumaluminium, nabízejí asi 10% úsporu hmotnosti oproti předchozím slitinám se srovnatelnou odolností proti střele, ačkoli balistický výkon musí být podle Total Materia ještě plně vyhodnocen.
Zlepšují se také metody svařování, včetně robotických. Mezi řešené úkoly patří minimalizace dodávky tepla, stabilnější svařovací oblouk díky zdokonalení systémů dodávek energie a drátu a také monitorování a řízení procesu expertními systémy.
Společnost MTL Advanced Materials spolupracovala s firmou ALCOA Defense, renomovaným výrobcem hliníkových pancéřových desek, na vývoji toho, co společnost popisuje jako „spolehlivý a opakovatelný proces tváření za studena“. Společnost poznamenává, že slitiny hliníku vyvinuté pro brnění nebyly navrženy pro tváření za studena, což znamená, že její nový proces by měl pomoci vyhnout se běžným režimům selhání, včetně praskání. Konečným cílem je umožnit konstruktérům strojů minimalizovat potřebu svařování a snížit počet dílů, uvádí společnost. Společnost zdůrazňuje snížení objemu svařování, zvyšuje strukturální pevnost a ochranu posádky při současném snížení výrobních nákladů. Počínaje osvědčenou slitinou 5083-H131 vyvinula společnost postup pro tváření dílů za studena s úhlem ohybu 90 stupňů podél a přes zrna, poté přešla na složitější materiály, například slitiny 7017, 7020 a 7085, také dosažení dobrých výsledků.
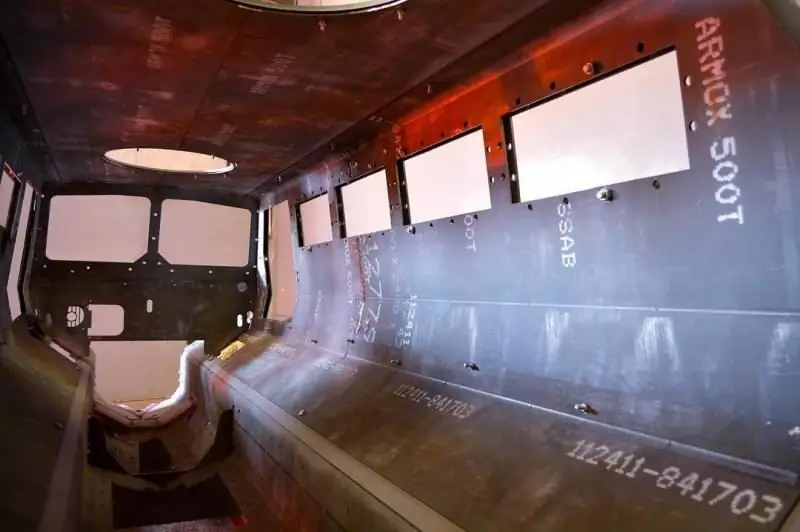
Keramika a kompozity
Před několika lety společnost Morgan Advanced Materials oznámila vývoj několika pancéřových systémů SAMAS, které sestávaly z kombinace pokročilé keramiky a strukturálních kompozitů. Produktová řada zahrnuje sklopné brnění, výstelky proti fragmentaci, kapsle na přežití vyrobené ze strukturálních kompozitů pro výměnu kovových trupů a ochranu zbraňových modulů, obydlených i neobydlených. Všechny lze přizpůsobit konkrétním požadavkům nebo vyrobit na zakázku.
Poskytuje ochranu STANAG 4569 úrovně 2-6 spolu s víceúčinovým výkonem a úsporou hmotnosti (společnost tvrdí, že tyto systémy váží polovinu oproti podobným ocelovým výrobkům) a přizpůsobuje se konkrétním hrozbám, platformám a misím …. Obložení proti třískám lze vyrobit z plochých panelů o hmotnosti 12,3 kg na pokrytí plochy 0,36 m2 (asi 34 kg / m2) nebo z pevných tvarovek o hmotnosti 12,8 kg na 0,55 m2 (asi 23,2 kg / m2).
Podle Morgan Advanced Materials nabízí další brnění určené pro nové a modernizace stávajících platforem stejné možnosti při poloviční hmotnosti. Patentovaný systém poskytuje maximální ochranu proti široké škále hrozeb, včetně zbraní malého a středního kalibru, improvizovaných výbušných zařízení (IED) a raketových granátů, jakož i výkonu při více nárazech.
„Polostrukturní“pancířový systém s dobrou odolností proti korozi je nabízen pro zbraňové moduly (kromě leteckých a námořních aplikací) a spolu s úsporou hmotnosti a minimalizací problémů s těžištěm na rozdíl od oceli vytváří méně problémů s elektromagnetickou kompatibilitou.
Zvláštním problémem je ochrana zbraňových modulů, protože jsou atraktivním cílem, protože jejich deaktivace drasticky zhoršuje velení posádky nad situací a schopnost vozidla vypořádat se s blízkými hrozbami. Mají také jemnou optoelektroniku a zranitelné elektromotory. Protože jsou obvykle instalovány v horní části vozidla, mělo by být pancéřování lehké, aby bylo těžiště co nejnižší.
Systém ochrany zbraňových modulů, který může zahrnovat pancéřové sklo a ochranu horní části, je zcela skládací, dvě osoby jej mohou znovu sestavit za 90 sekund. Kompozitní kapsle na přežití jsou vyrobeny z toho, co společnost popisuje jako „jedinečné houževnaté materiály a polymerní formulace“, poskytují ochranu proti šrapnelu a lze je opravit v terénu.
Ochrana vojáka
Systém SPS (Soldier Protection System) vyvinutý společností 3M Ceradyne obsahuje přilby a vložky v neprůstřelné vestě pro integrovaný systém ochrany hlavy (IHPS) a VTP (ochrana životně důležité části trupu) - komponenty ESAPI (Enhanced Small Arms Protective Insert) - vylepšená vložka pro ochranu před ručních palných zbraní) systému SPS.
Mezi požadavky IHPS patří lehčí váha, pasivní ochrana sluchu a vylepšená ochrana proti otřesům. Systém také zahrnuje příslušenství, jako je součást chránící spodní čelist vojáka, ochranný štít, držák na brýle pro noční vidění, vodítka například pro baterku a kameru a dodatečnou modulární ochranu před kulkou. Smlouva v hodnotě více než 7 milionů dolarů počítá s dodávkou zhruba 5300 přileb. Mezitím bude v rámci smlouvy na 36 milionů dolarů dodáno více než 30 000 souprav ESAPI - lehčích vložek do neprůstřelných vest. Výroba obou těchto stavebnic byla zahájena v roce 2017.
Také v rámci programu SPS vybrala KDH Defence materiály Honeywell SPECTRA SHIELD a GOLD SHIELD pro pět subsystémů, včetně subsystému Torso and Extremity Protection (TEP), který bude dodán pro projekt SPS. Ochranný systém TEP je o 26% lehčí, což v konečném důsledku snižuje hmotnost systému SPS o 10%. KDH bude ve svých vlastních produktech pro tento systém používat SPECTRA SHIELD, který je založen na vlákně UHMWPE, a GOLD SHIELD, založený na aramidových vláknech.
Vlákno SPECTRA
Společnost Honeywell využívá patentovaný proces zvlákňování a tažení polymerních vláken k vložení suroviny UHMWPE do vlákna SPECTRA. Tento materiál je z hlediska hmotnosti 10krát pevnější než ocel, jeho specifická pevnost je o 40% vyšší než u aramidových vláken, má vyšší bod tání než standardní polyetylen (150 ° C) a ve srovnání s jinými polymery má vyšší odolnost proti opotřebení, např. například polyester.
Pevný a tuhý materiál SPECTRA vykazuje vysokou deformaci při přetržení, to znamená, že se před zlomením velmi silně natáhne; tato vlastnost umožňuje absorbovat velké množství energie nárazu. Honeywell tvrdí, že vláknové kompozity SPECTRA fungují velmi dobře při nárazech vysokou rychlostí, jako jsou střely do pušek a rázové vlny. Podle společnosti „Naše pokročilé vlákno reaguje na náraz rychlým odstraněním kinetické energie z nárazové zóny … má také dobré tlumení vibrací, dobrou odolnost proti opakovaným deformacím a vynikající vlastnosti vnitřního tření vláken spolu s vynikající odolností vůči chemikáliím, voda a UV světlo. “
Honeywell ve své technologii SHIELD šíří paralelní vlákna vláken a spojuje je dohromady impregnací vyspělou pryskyřicí a vytváří jednosměrnou pásku. Poté jsou vrstvy této pásky umístěny příčně v požadovaných úhlech a při dané teplotě a tlaku, pájeny do kompozitní struktury. Pro aplikace měkkého nošení je laminován mezi dvě vrstvy tenké a pružné průhledné fólie. Protože vlákna zůstávají rovná a rovnoběžná, rozptylují energii nárazu efektivněji, než kdyby byla vetkána do tkaniny.
Short Bark Industries také používá SPECTRA SHIELD v bodyguardu BCS (Ballistic Combat Shirt) pro systém SPS TEP. Short Bark se specializuje na měkkou ochranu, taktické oděvy a doplňky.
Podle Honeywella si vojáci vybrali ochranné prvky vyrobené z těchto materiálů poté, co prokázali vynikající výkon oproti svým protějškům z aramidových vláken.